Enhancing Production Efficiency in Plastic Processing with Nano Heating Technology
9/1/20244 min read
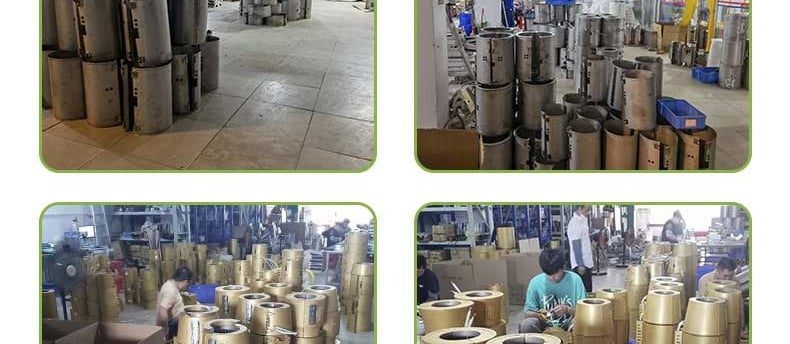
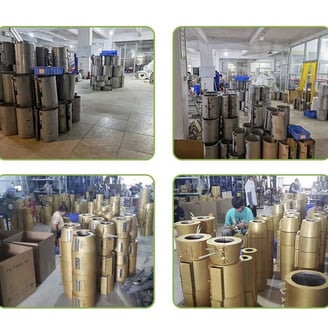
```html
Understanding Nano Heating Technology
Nano heating technology represents a revolutionary advancement in the realm of thermal processing, particularly within the plastics industry. At its core, nano heating technology utilizes nanoparticles, which are materials with dimensions on the nanometer scale, to generate heat when exposed to certain stimuli such as electromagnetic fields. These nanoparticles, often composed of materials like carbon nanotubes or metallic nanoparticles, exhibit unique thermal properties that enable rapid and efficient heating.
The principle behind nano heating technology is fundamentally different from conventional heating methods. Traditional systems often rely on resistive heating elements or convection mechanisms, which can be slow and energy-intensive. In contrast, nano heating technology provides direct heating at the molecular level, ensuring an unprecedented precision and control. This process not only reduces the time required to reach the desired temperature but also significantly minimizes energy consumption. Additionally, the localized heating capability of nano systems ensures uniform temperature distribution, thereby reducing thermal gradients and preventing degradation of materials.
The development of nano heating technology has paved the way for creating highly specialized heating solutions tailored to the needs of various industries. In plastic processing, for instance, the enhanced control and efficiency offered by nano heaters allow for more consistent product quality and extended equipment life. The rapid heating response also facilitates faster production cycles, contributing to higher overall productivity.
When compared to traditional heating methods, the benefits of nano heating technology become strikingly evident. Traditional systems often involve substantial energy wastage and lack precise control, leading to potential overheating and inefficiencies. Conversely, nano heating systems excel in providing optimal thermal management, resulting in lower operational costs and improved sustainability. The reduction in energy consumption not only fosters economic advantages but also aligns with global efforts towards environmental conservation.
```Applications of Nano Heating Technology in Plastic Processing
Nano heating technology has been emerging as a revolutionary catalyst for enhancing production efficiency across various stages of plastic processing. Its implementation spans injection molding, extrusion, and blow molding, each benefiting significantly from the unique attributes nano heating offers.
In injection molding, the precision control facilitated by nano heating technology has led to remarkable improvements in cycle times and energy consumption. The ability to uniformly heat molds ensures a consistent temperature throughout, which directly translates to superior quality in the final products. Industries integrating nano heating technology in injection molding report a 20-30% reduction in cycle times and up to 25% savings in energy costs.
Extrusion processes also see considerable enhancements from nano heating technology. The uniformly distributed heat within extruders allows for a smoother and more consistent flow of the plastic material, mitigating common issues such as flow marks and warping. Examples from the packaging industry have shown a substantial decrease in material inconsistencies and a 15% reduction in production waste, significantly optimizing resource utilization.
Similarly, blow molding benefits from the rapid and precise temperature control afforded by nano heating technology. This control is crucial for forming high-quality hollow plastic parts with uniform wall thickness. Case studies from the automotive sector highlight that implementing nano heating technology can lead to up to 20% improvements in product uniformity and a notable reduction in cycle times by approximately 15-20%, substantially raising overall production efficiency.
Moreover, the comprehensive application of nano heating technology addresses sustainability concerns within the plastic industry. By reducing energy consumption and material waste, companies are not only achieving economic benefits but also contributing to environmental sustainability. Enhanced material properties, such as increased strength and durability, further cement the role of nano heating as a pivotal technology in modern plastic processing.
Implementing Nano Heating Technology in Existing Production Systems
The integration of nano heating technology into existing plastic processing systems necessitates a structured approach to ensure seamless adoption and maximize benefits. The initial phase encompasses a thorough assessment of the current equipment and processes. This evaluation identifies compatibility issues and areas where nano heating can bring immediate improvements in efficiency. Following the assessment, a detailed planning phase is crucial to outline the implementation process, including timelines, budget considerations, and resource allocation.
During the installation phase, it is vital to engage with experts specializing in nano heating technology. Their expertise ensures that the installation is executed correctly, reducing downtime and mitigating risks of potential disruptions. Post-installation, calibration is essential to fine-tune the equipment for optimal performance. Routine calibration schedules should be established to maintain the efficiency of the newly installed technology.
A significant challenge in the implementation process is the compatibility of nano heating technology with existing systems. Retrofitting might be necessary in some cases, requiring modifications to integrate seamlessly with current equipment. Another critical aspect is the need for employee training. Investing in comprehensive training programs equips staff with the necessary skills to operate and maintain the new technology, ensuring smooth and efficient operations.
Conducting a cost-benefit analysis is paramount to justify the initial investment in nano heating technology. Though the upfront costs may be substantial, the long-term savings and efficiency gains are considerable. Enhanced production speed, reduced energy consumption, and lower maintenance costs contribute to a favorable return on investment. Additionally, the implementation can lead to improved product quality and consistency, further enhancing profitability.
Looking ahead, advancements in nano heating technology hold exciting prospects for the plastic processing industry. Emerging trends suggest continued improvements in energy efficiency and heating precision, paving the way for even greater production optimization. Staying abreast of these developments can offer a competitive edge and ensure sustained growth and innovation in plastic processing operations.
Innovate
Custom electric heating solutions for diverse industries.
Quality
Service
+86-13600007673
© 2024. All rights reserved.