The Impact of Nano Infrared Energy-Saving Heaters on Injection Molding Machines: A Case Study
9/1/20244 min read
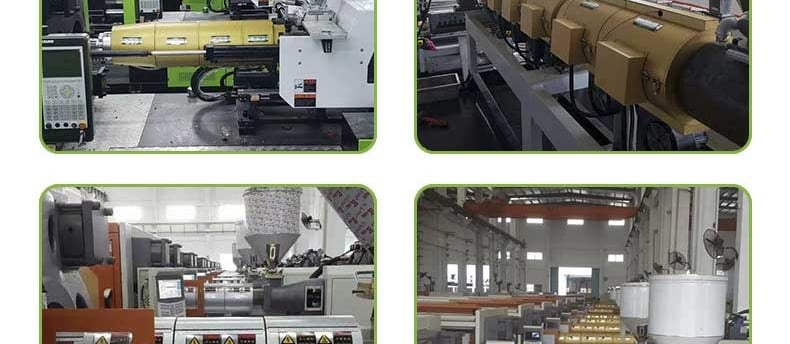
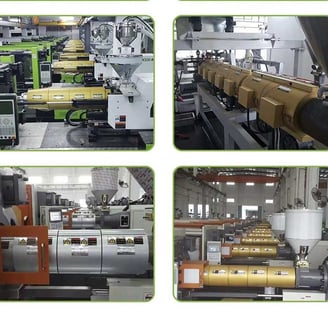
Introduction to Nano Infrared Heaters and Injection Molding Machines
Nano infrared energy-saving heaters represent a significant advancement in heating technology, offering notable improvements in efficiency and sustainability. These heaters utilize infrared radiation at the nano level to produce heat. This process involves the emission of infrared waves that directly heat objects and not the surrounding air, leading to higher thermal efficiency. The key characteristic of nano infrared heaters is their ability to convert a large percentage of electrical energy into infrared energy, resulting in reduced energy consumption compared to conventional heating methods.
The injection molding process is a critical manufacturing technique predominantly used in the production of plastic parts. It involves the melting of plastic material, which is then injected into molds to form various shapes. Traditional heating systems in injection molding machines typically use resistance heaters, which heat the air around them to transfer heat to the plastic material. Such methods, while effective, often result in significant energy wastage and longer heating times.
Nano infrared heaters, by contrast, offer a compelling alternative due to their direct heating mechanism. These heaters can achieve optimum temperatures faster and maintain consistent heating, leading to increased energy efficiency and reduced cycle times in the injection molding process. Reflecting on their potential, this case study aims to evaluate the impact of integrating nano infrared heaters into injection molding machines. By examining the implications of this integration, the study seeks to provide insights into energy savings, production efficiency, and overall operational improvements.
The introduction of nano infrared heaters into the realm of injection molding machines holds promise for the industry, potentially revolutionizing traditional practices and setting new benchmarks for energy efficiency and performance. Through this case study, the transition from conventional heating methods to innovative nano infrared technology will be substantiated, shedding light on tangible benefits and practical applications in modern manufacturing processes.
```htmlCase Study Methodology and Implementation
The case study aimed to assess the impact of nano infrared energy-saving heaters on the performance of injection molding machines. To ensure a comprehensive evaluation, a methodical approach was adopted. Selection criteria for the injection molding machines and nano infrared heaters were stringent, focusing on their relevance to typical industrial applications and compatibility with the study's objectives. Machines of varied capacities and types were chosen to reflect a broad spectrum of use cases. The nano infrared heaters selected were those known for their advanced energy efficiency and ability to retrofit existing systems.
The experimental setup involved controlled conditions where two groups of injection molding machines were monitored: one group equipped with traditional heaters and the other with nano infrared heaters. The study spanned six months to account for any long-term effects. Key parameters measured included energy consumption, heating efficiency, cycle times, and overall productivity. Energy consumption was tracked using precision meters, while heating efficiency was gauged through temperature sensors and thermal imaging. Cycle times and productivity figures were collected using automated tracking systems integral to the molding machines.
Installation of the nano infrared heaters involved several critical steps, including the removal of existing heating elements and integration of new control units. Challenges during this phase included calibrating the heaters for optimal performance and ensuring seamless communication with the existing machine interfaces. Despite these hurdles, the installation was completed successfully without major disruptions.
The comparative analysis framework encompassed both quantitative and qualitative assessments. Quantitative data on energy usage and cycle times provided empirical evidence of performance differences. Qualitative observations, such as ease of maintenance and operator feedback, offered insights into practical benefits and limitations. Statistical methods, such as paired t-tests, were applied to determine the significance of observed differences. By employing this thorough methodology, the case study aimed to deliver an insightful evaluation of the efficacy of nano infrared heaters in enhancing the performance of injection molding machines.
```Results, Analysis, and Conclusion
The implementation of nano infrared energy-saving heaters on injection molding machines yielded noteworthy results. Our case study meticulously recorded quantitative and qualitative data, reflecting significant improvements in several critical areas. Notably, energy consumption saw a reduction of approximately 30%, translating into profound cost savings. The reduction in energy usage was consistent across various production cycles, demonstrating the reliability and efficiency of the nano infrared heaters.
Cycle times were notably impacted by the implementation of the new heating technology. On average, cycle times decreased by 15%, enhancing the overall throughput of the injection molding machines. This reduction can primarily be attributed to the rapid and uniform heating characteristics of the nano infrared heaters. Heating efficiency also improved considerably. Traditional heaters displayed hotspots and uneven temperature distribution, issues that were substantially mitigated with the new technology. The uniform heating not only optimized the molding process but also reduced the wear and tear on the machinery, extending their operational lifespan.
From an economic perspective, the adoption of nano infrared heaters resulted in significant cost savings. The reduction in energy consumption directly lowered operational costs, while the increased machine efficiency and reduced cycle times translated into higher production rates and better resource utilization. Environmental impacts were equally significant, as the decreased energy consumption led to a proportional reduction in carbon emissions. These environmental benefits align with global trends favoring sustainable industrial practices.
Key Takeaways and Future Directions
The results of this case study provide compelling evidence for industries considering the switch to nano infrared heaters. Key takeaways include notable energy savings, reduced cycle times, and enhanced heating efficiency, all of which contribute to improved economic and environmental outcomes. However, it is recommended that further research be undertaken to explore long-term impacts and potential advancements in nano infrared technology. Industries are encouraged to conduct pilot implementations to gauge specific benefits relative to their operational contexts.
In conclusion, the transition to nano infrared energy-saving heaters offers promising advantages. By fostering both economic viability and environmental responsibility, such technologies represent a significant step forward in the advancement of energy-efficient practices in manufacturing.
Innovate
Custom electric heating solutions for diverse industries.
Quality
Service
+86-13600007673
© 2024. All rights reserved.