Nano Heaters in Extruders: The Key to Optimizing Production Processes
9/1/20244 min read
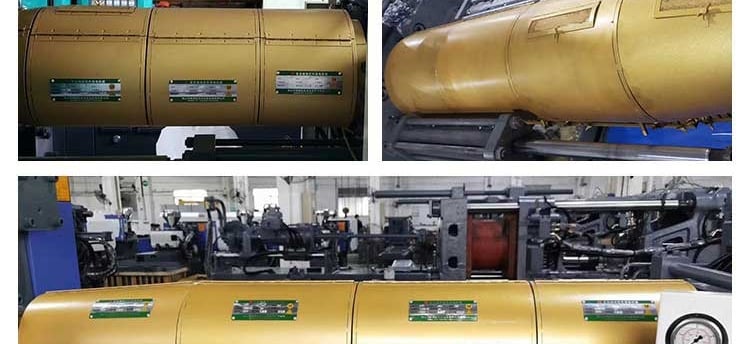
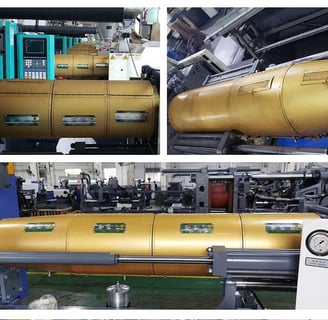
Introduction to Nano Heaters and Their Role in Extruders
Nano heaters represent a significant advancement in thermal management technologies, particularly in their application within extruders. At a fundamental level, nano heaters operate by exploiting the exceptional thermal conductivity properties of nanoscale materials. These heaters generate and distribute heat with a precision unattainable by conventional heating elements. The ability to control temperature with such accuracy allows for significant improvements in efficiency and product quality, making nano heaters a pivotal component in modern manufacturing processes.
Extruders, essential machinery in industries such as plastics manufacturing, food production, and pharmaceuticals, benefit immensely from the integration of nano heater technology. The primary function of an extruder is to manipulate raw materials through a combination of heat and mechanical force, transforming them into finished products. Traditional heaters in extruders often face challenges related to inefficient heat distribution and energy consumption. With nano heaters, these issues are effectively mitigated. The precise and uniform heat distribution leads to consistent extrusion quality and significantly reduces energy wastage.
The unique advantages that nano heaters introduce to extruder technology are numerous. Precise temperature control ensures that thermally sensitive materials are processed correctly, enhancing the structural and functional integrity of the end products. Additionally, the energy savings attributed to the enhanced thermal efficiency of nano heaters contribute to a reduction in operational costs and a lower environmental footprint. This, coupled with the ability to maintain consistent quality, makes nano heaters invaluable in modern extrusion processes.
Furthermore, the application of nano heaters extends the longevity and reliability of extruders. Traditional heaters often necessitate frequent maintenance due to wear and uneven heating. In contrast, nano heaters provide stable and uniform thermal conditions, thereby minimizing the stress on the extruding components. This leads to reduced downtime and increased productivity, underscoring the importance of nano heaters in optimizing production processes across various industries.
Benefits of Integrating Nano Heaters in Production Processes
Integrating nano heaters in extruders offers a myriad of benefits, which significantly enhance production processes. One of the primary advantages is the ability to maintain consistent heating throughout the manufacturing cycle. Consistent heating ensures uniformity in product quality, particularly crucial in industries such as the manufacturing of high-precision plastic components where even minor temperature fluctuations can lead to defects and variability in the final products.
Another significant benefit is the reduction in energy consumption. Nano heaters are designed to be highly efficient, converting a larger percentage of energy into heat and reducing waste. This efficiency translates into lower energy costs, which is particularly beneficial in energy-intensive manufacturing sectors. Furthermore, by ensuring optimal energy usage, nano heaters contribute to a more sustainable production process, aligning with global efforts to reduce industrial carbon footprints.
Minimizing material wastage is another critical advantage offered by nano heaters. In the production of heat-sensitive food items, for example, precise temperature control is vital to prevent degradation of the product. Nano heaters enable meticulous management of heat distribution, ensuring that raw materials are utilized to their maximum potential and reducing instances of overcooking or undercooking.
Several case studies and research findings underscore the quantitative improvements brought about by integrating nano heaters in extruders. For instance, in the plastic manufacturing industry, companies have reported up to a 15% increase in production efficiency and a 20% reduction in energy costs. These improvements are attributed to the precise control over the extrusion process afforded by nano heaters. Similarly, food production facilities have observed enhanced product uniformity and significant decreases in material wastage, leading to substantial cost savings.
In conclusion, the benefits of integrating nano heaters in extruders are profound, offering consistent heating, reduced energy consumption, and minimized material wastage. These advantages not only optimize production processes but also contribute to cost savings and product excellence, making nano heaters a valuable asset in various industries.
Challenges and Future Prospects of Nano Heater Technology
The integration of nano heater technology in extruders faces several challenges that need to be addressed to optimize its adoption. One significant impediment is the technological limitations inherent to nano heaters themselves. While these heaters offer precise control and energy efficiency, their production and implementation require advanced materials and manufacturing techniques, which are presently not widespread. The complexity of fabricating nano-scale components poses hurdles that can impede large-scale deployment.
Another notable challenge is the substantial initial investment costs. Incorporating nano heater technology into existing production frameworks necessitates substantial financial outlay. Businesses must consider the cost of not only the nano heaters but also the requisite adjustments to their extruder systems. This financial barrier can deter smaller enterprises, limiting widespread adoption across various industries.
Maintenance and reliability issues also present considerable challenges. The miniature scale of nano heaters means they are susceptible to damage and may require more meticulous maintenance routines compared to traditional heaters. Potential malfunctions or degradation over time could lead to increased downtime and maintenance expenses, impacting overall production efficiency.
Future Prospects and Technological Advancements
Despite these challenges, ongoing research and technological advancements provide promising prospects for the future of nano heater technology in extruders. Significant strides are being made in material science, aiming to develop more robust and durable nano components. Advancements in manufacturing techniques, such as additive manufacturing and nano-printing, are also anticipated to reduce production costs and complexity, making the technology more accessible.
Looking ahead, potential innovations could vastly broaden the application of nano heaters. Enhanced durability and reduced costs are expected to make nano heaters viable for a wider range of industries, from pharmaceuticals to aerospace, where precision and efficiency are critical. Industry experts project that within the next decade, nano heater technology could become a standard feature in extruder systems, driven by continuous improvement and integration efforts.
The impact of these advancements on future production processes cannot be overstated. Improved thermal management and energy efficiency can significantly enhance production speed, product quality, and overall operational cost-effectiveness. As more companies recognize the long-term benefits, the industry is likely to see a progressive shift towards adopting nano heaters, significantly optimizing production processes globally.
Innovate
Custom electric heating solutions for diverse industries.
Quality
Service
+86-13600007673
© 2024. All rights reserved.