Applications and Advantages of Nano Ceramic Heaters in the Plastic Processing Industry
9/1/20244 min read
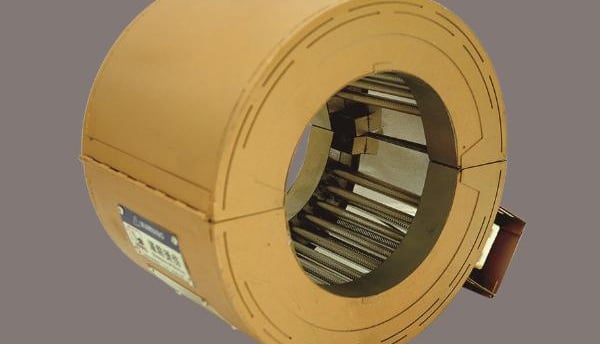
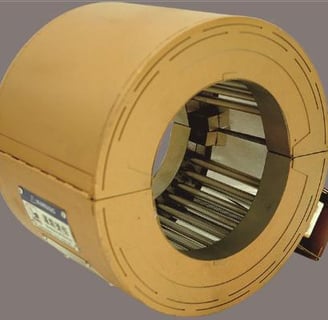
Nano ceramic heaters represent a significant advancement in heating technology, characterized by their unique composition and efficiency. These heaters utilize nanotechnology to produce heating elements that offer a range of superior properties compared to traditional heating elements. At the core, nano ceramic heaters are composed of ceramic materials embedded with nanoscale particles that enhance their heat conduction and thermal properties.
The working principles of nano ceramic heaters are centered around these nanoscale particles, which enable rapid and efficient heat transfer. When an electric current passes through the heating element, the nano particles rapidly respond, producing heat uniformly across the surface. This rapid heating capability ensures that nano ceramic heaters reach their target temperatures much faster than conventional metal or alloy heaters.
One of the standout features of nano ceramic heaters is their high thermal efficiency. The integration of nanotechnology allows these heaters to achieve optimal thermal performance with minimal energy wastage. The even heat distribution characteristic of nano ceramic heaters prevents the occurrence of hot spots, which can be detrimental in plastic processing by causing material degradation or uneven processing. This even distribution also contributes to maintaining consistent processing conditions, crucial for high-quality plastic product manufacturing.
Durability is another critical aspect where nano ceramic heaters excel. The materials used in their construction are highly resistant to oxidation and degradation, even at elevated temperatures. This resistance to wear and tear ensures a longer operational lifespan, reducing maintenance requirements and downtime in industrial settings.
In terms of industrial applications, nano ceramic heaters offer distinct advantages particularly in the plastic processing industry. Their rapid heating, high efficiency, and durability make them an ideal choice for processes that demand precise temperature control and consistent heating. These benefits, powered by underlying nanotechnology, underscore the pivotal role nano ceramic heaters are poised to play in advancing industrial heating solutions.
```html
Applications of Nano Ceramic Heaters in Plastic Processing
The integration of nano ceramic heaters has revolutionized the plastic processing industry by enhancing precision, energy efficiency, and thermal consistency across various production stages. One of the primary applications of these advanced heaters is in injection molding. In this process, nano ceramic heaters ensure that the plastic material reaches its optimal melting point swiftly and maintains a uniform temperature throughout the molding phase. This consistency translates into higher quality molded products with reduced incidences of defects and improved structural integrity.
Another critical application is in extrusion, where plastic materials are forced through a shaped die to produce continuous profiles such as pipes, sheets, or films. Nano ceramic heaters play a vital role in maintaining the exact temperature needed for the plastic's malleability and flow. By delivering precise thermal control, these heaters minimize material wastage and energy consumption, highlighting their significance in sustainable manufacturing processes.
In the domain of thermoforming, where plastic sheets are heated and formed over a mold, nano ceramic heaters ensure even heating distribution. This uniformity is crucial in preventing warping or uneven thickness, guaranteeing that the final products meet stringent quality standards. The rapid and precise heating capabilities of nano ceramic heaters also reduce cycle times, thereby boosting production efficiency.
Real-world examples underscore the effectiveness of nano ceramic heaters in plastic processing. For instance, a leading manufacturer utilizing these heaters in their injection molding operations reported a significant reduction in energy usage by approximately 30%, while also achieving a 15% increase in production speed. Similarly, a company specializing in thermoforming observed a marked improvement in product consistency and a substantial decrease in defect rates post-implementation of nano ceramic heaters.
These case studies illustrate not only the broad acceptance of nano ceramic heaters in industrial settings but also their tangible impact on operational efficiencies and product quality. As the plastic processing industry continues to prioritize sustainability and precision, the adoption of nano ceramic heaters is poised to expand further, cementing their role as a cornerstone of modern manufacturing practices.
```
Advantages of Using Nano Ceramic Heaters
Nano ceramic heaters have emerged as a pivotal technology in the plastic processing industry, offering a myriad of advantages that significantly enhance production quality and efficiency. One of the most notable benefits of nano ceramic heaters is their energy efficiency. These heaters utilize advanced materials and innovative designs to achieve rapid heating and precise temperature control, thereby consuming less energy compared to traditional heating systems. This substantial reduction in energy consumption contributes directly to lower operational costs, making the entire production process more cost-effective.
In addition to energy savings, nano ceramic heaters are renowned for their extended lifespan. The durability of nano ceramic materials ensures that these heaters can withstand the high temperatures and rigorous conditions typical of plastic processing environments. This longevity minimizes the frequency of replacements and repairs, further reducing maintenance costs and downtime.
Another critical advantage of nano ceramic heaters is their ability to enhance production quality. Consistent and accurate temperature control is essential in plastic processing to avoid defects and ensure uniformity in the final products. Nano ceramic heaters excel in providing stable and controlled heating, which translates to higher quality products and fewer rejects.
Environmental sustainability is an additional benefit that cannot be overlooked. The reduced energy consumption of nano ceramic heaters leads to a smaller carbon footprint, aligning with global efforts to minimize industrial impact on the environment. Moreover, the use of durable materials means less frequent disposal of old heaters, contributing to waste reduction.
Safety improvements are another significant advantage. The reduced risk of overheating and precise temperature management inherent in nano ceramic heaters mitigate potential hazards associated with thermal runaway or uneven heating. This not only ensures the safety of the equipment but also protects workers from potential injuries.
Overall, the integration of nano ceramic heaters in plastic processing operations delivers a comprehensive suite of benefits, ranging from economic savings and enhanced product quality to improved sustainability and safety. These advantages make nano ceramic heaters an invaluable asset in modern plastic processing facilities.
Innovate
Custom electric heating solutions for diverse industries.
Quality
Service
+86-13600007673
© 2024. All rights reserved.